Metallographic Methods
Excerpted from International Atlas of Powder Metallurgical Microstructures
Metallographic preparation and inspection of powder metallurgical materials is a specific sector of general metallography. Therefore, standard handbooks should be consulted in the usual way also for powder metallurgical work. However, there is one peculiar aspects, which requires special attention: characterization and preservation of porosity in powder metallurgical materials.
Preparation and Characterization of Materials Containing Residual Porosity Metallographic preparation of a porous material can lead to changes in the specimen surface which will cause erroneous interpretation of the microstructure. This is illustrated in Fig. XVI. Partial closure of pores can be caused by plastic deformation of material during grinding and polishing. Fig. XVIa and c. Fig. XVIb illustrates the breaking of pore edges around the pore periphery of brittle materials. Also rounding of pore edges may occur during grinding and polishing or by chemical attack during etching. This is schematically shown in Fig. XVId.
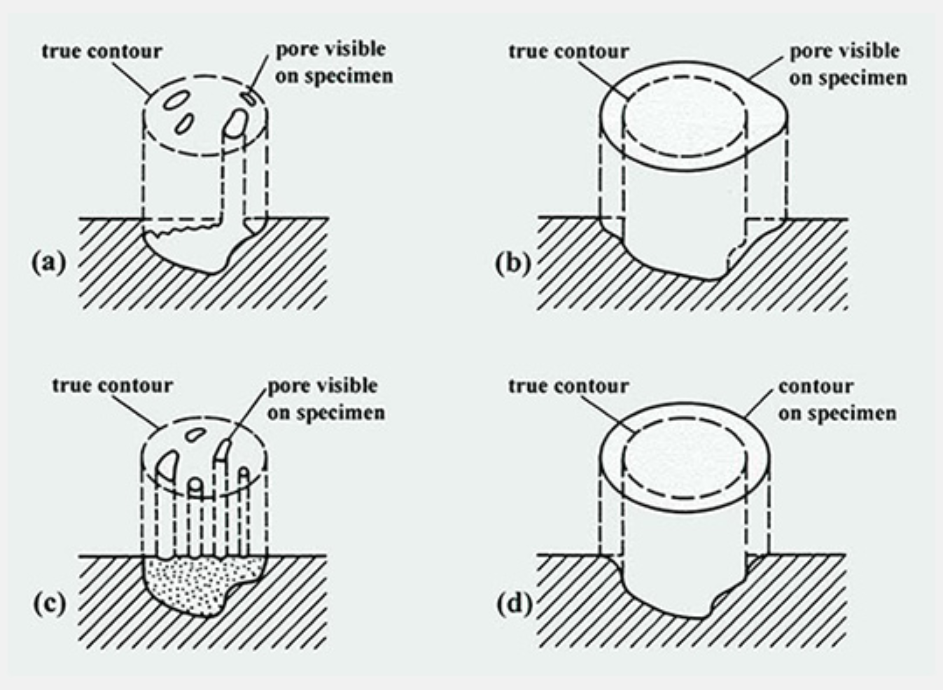
Fig. XVI: Potential mistakes during metallographic preparation of materials containing residual porosity
a) partial closing of pores by plastic deformation during grinding
b) break-out of material around pore
c) closing of pores during polishing
d) rounding of pore edges during polishing and etching
Specimens are obtained by sectioning with an abrasive wheel under water as a coolant. In order to remove cutting debris from the pores, thorough ultrasonic cleaning and rinsing with water is mandatory. The water is repelled from the pores in white spirit under ultrasonic agitation.
Depending on requirements two alternatives for sample preparation are suggested. The first relates to the resolution of the microstructure, the second is meant for quantitative image analysis of porosity investigations.
Microstructure
- Mounting: Samples are hot embedded in resin suing molds of 25.4 mm diameter at 180 °C for 10 min with a load of about 30 kN.
- Grinding: In a first step, samples are ground for 2 min on magnetic discs type MD–Piano with a grit size of 80, followed by a second grinding operation with a grit size of 120 for 3 min. The load per sample should be selected between 25 and 50 N at a speed of 300 rpm
- Polishing: Three subsequent steps have proven to yield satisfactory results, first an MD–Large disc with 9 µm diamond suspension is applied for 10 min, followed by an MD–Dac cloth with 3 µm diamond suspension for 8 min, and finally an MD–Nap cloth with a 1 µm diamond suspension is used for 4 min. The load is the same as during grinding, with a speed of 150 rpm. After each individual preparation step thorough ultrasonic cleaning is absolutely essential.
- Etching is generally performed by immersion. Table 1 summarizes own experience and information from the literature and lists the most commonly used etchants for powder metallurgical materials. Quantitative Image Analysis of Pores
- Impregnation: Prior to mounting, the interconnected porosity must be vacuum impregnated with resin.
- Mounting: Samples are hot embedded in glass fiber or particle reinforced resins for increased edge retention.
- Grinding: With densities below about 7 g/cm3 grinding is performed as in the previous recipe. With higher densities silicon carbide papers with grit sizes up to 1200 are preferred. In this case, all grinding steps are carried out with 300 rpm under a load of 15 N per sample for 2 to 3 min each.
- Polishing: Lower densities are polished as in the previous recipe. For higher densities a difference approach is preferred. For the first three steps self adhesive perforated Texmet P cloths on metallic discs are used with 30, 15 and 9 µm diamond paste. The alcoholic cooling fluid contains 0.05 vol.% HNO3. Between 15 and 9 µm polish an intermediate nital etch is recommended. The remaining steps are carried out with 6, 3 and 1 µm diamond suspension on silk cloth with a total time of about 25 min. The cooling fluid must be free of HNO3. All steps take place at 150 rpm with 20 N load per sample. If necessary, a final buff with silicon oxide polishing suspension is applied for about 10 s. For evaluations of pore size and morphology, etching has negative effects.
Quantitative Image Analysis of Pores
- Impregnation: Prior to mounting, the interconnected porosity must be vacuum impregnated with resin.
- Mounting: Samples are hot embedded in glass fiber or particle reinforced resins for increased edge retention.
- Grinding: With densities below about 7 g/cm3 grinding is performed as in the previous recipe. With higher densities silicon carbide papers with grit sizes up to 1200 are preferred. In this case, all grinding steps are carried out with 300 rpm under a load of 15 N per sample for 2 to 3 min each.
- Polishing: Lower densities are polished as in the previous recipe. For higher densities a difference approach is preferred. For the first three steps self adhesive perforated Texmet P cloths on metallic discs are used with 30, 15 and 9 µm diamond paste. The alcoholic cooling fluid contains 0.05 vol.% HNO3. Between 15 and 9 µm polish an intermediate nital etch is recommended. The remaining steps are carried out with 6, 3 and 1 µm diamond suspension on silk cloth with a total time of about 25 min. The cooling fluid must be free of HNO3. All steps take place at 150 rpm with 20 N load per sample. If necessary, a final buff with silicon oxide polishing suspension is applied for about 10 s. For evaluations of pore size and morphology, etching has negative effects.

Disclaimer: The contents of this website are intended to be used as a reference for educational and/or comparison purposes. No position should be taken by the user with respect to the validity of the contents of the website. For verification, the user should seek the opinion of a certified laboratory. Neither MPIF nor any of its members assumes or accepts any liability resulting from the use of this website.