Keynote Presentation
Megatrends in Near Net Shape Manufacturing
Dr. Diran Apelian - Distinguished Professor, MSE, Director, ACRC @ UCI
Diran Apelian is Distinguished Professor of MSE at the University of California, Irvine, where he is Director of the Advanced Casting Research Center (ACRC) and Associate Director of IDMI – Metal Processing. He is Provost Emeritus and Founding Director of the Metal Processing Institute at WPI, Worcester, Mass.
He received his B.S. degree in metallurgical engineering from Drexel University in 1968 and his doctorate in materials science and engineering from MIT in 1972. Apelian is a Fellow of TMS, ASM, and APMI; he is a member of the National Academy of Engineering (NAE), National Academy of Inventors (NAI), the European Academy of Sciences, the Armenian Academy of Sciences, and the Chinese Academy of Sciences. Apelian is the co-founder of Ascend Elements Inc., Solvus Global LLC, , and Melt Cognition LLC.
It is quite clear that in the 21st century we will need to reinvigorate our efforts to lightweight our infrastructure, reduce carbon footprint during manufacturing, reduce production waste, and recover post-consumer waste and upcycle. Manufacturing is at an inflection point with the advent of data science, digital manufacturing, Industry 4.0, and the changes we are experiencing in the future of work and the worker. In this presentation, the changes we anticipate in near net shape manufacturing will be reviewed and highlighted covering key industries: transportation, housing and architecture, energy production, batteries, fuel cells, electronics, and medical devices. The role of Policy is pivotal as it influences the megatrends that are envisioned. This presentation highlights the policies that need to be shaped by the voice of engineers and technologists to ensure a competitive and a sustainable future.
Powder Injection Molding Tutorial
Matthew Bulger, ATPM Consulting
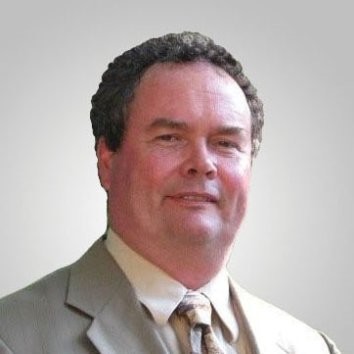
Matt has been involved in the area of metal injection molding (MIM) for more than 30 years. Matt received his MS in Materials Science from Rensselaer Polytechnic Institute and a BS in Physics from Carnegie – Mellon. In 2017, Matt received MPIF’s Distinguished Service to Powder Metallurgy Award which recognized his long-term contributions and achievements to the PM industry. Matt has been very involved with MPIF throughout his career, holing the offices of MPIF President and MIMA President (Metal Injection Molding Association) President, and MIMA Standards Chairman.
Currently Matt is with atpmconsulting. Prior to forming his consultant business, Matt held positions with NetShape Technologies – MIM, as the MIM General Manager, FloMet as the Quality & Materials Engineering Manager, and Remington Arms as a Process Engineer. In addition to instructing the Powder Injection Molding Tutorial at the International Conferences on Injection Molding of Metals, Ceramics and Carbides, Matt is has instructed at MPIF’s PM Sintering Seminars.
Gate Size in Metal Injection Molds
Griffin Seidler, Ruger Precision Metals
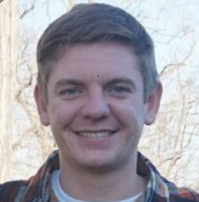
Griffin Seidler is a Process Engineer with Ruger Precision Metals, a division of Ruger Firearms. Griffin attended Missouri University of Science and Technology, graduating with a Bachelor’s of Science in Mechanical Engineering. After interning for RPM in college, he was hired on full time as a Manufacturing Engineer in charge of components for various firearm platforms. His scientific approach to resolving metal injection molding issues landed him in his current role, where he works to improve RPM’s MIM process and part quality.
Atomization and Characterization of Ferromagnetic Powders for MIM
John Johnson, FAPMI, Novamet/Ultra Fine Specialty Products
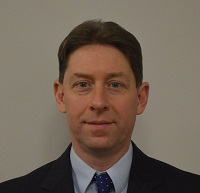
Dr. Johnson joined Novamet in 2020 as Vice President of Operations and Technology for both Novamet and Ultra Fine Specialty Products. Prior to joining Novamet, he was Vice President of Technology at Elmet Technologies. He previously held various R&D positions at ATI Firth Sterling, Kennametal, Singapore Technologies, Alcoa, Howmet, and Penn State. He has a B.S. from Virginia Tech, a M.S. from Rensselaer Polytechnic Institute, and a Ph.D. from Penn State. He is the Roadmap Chairman for the MPIF Technical Board and was awarded APMI Fellow status in 2019.
Hot Disk Thermal Characterization of MIM Parts at Every Production Stage
Artem Trofimov, Orton Ceramic Foundation
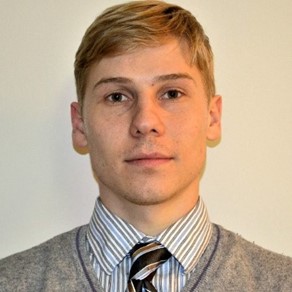
Artem is from Odintsovo, Moscow region, Russia. He graduated from Russian State University of Aviation Technology in 2012 with B.S./M.S. in physics. The same year he joined Clemson University where he received his M.S. degree in 2014 and Ph.D. in 2018 both in materials science and engineering. His Ph.D. research was focused on ceramic scintillators. Following completion of his Ph.D., Artem joined Oak Ridge National Laboratory in 2018 as a Postdoctoral Fellow working in the area of thermophysics and thermal characterization of materials. After finishing his fellowship at ORNL in summer 2021, Artem secured a position at Orton Ceramic Foundation continuing his work in the field of thermophysics and materials characterization.
Review of Some Sinter-Based Metal Additive Manufacturing Technologies
Animesh Bose, FAPMI, Desktop Metal
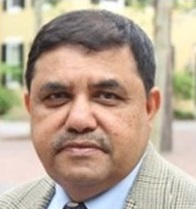
Dr. Animesh Bose has been involved in the area of powder metallurgy (PM) for more than 40 years.
He has published over 125 papers, 10 patents, and 4 books. He currently serves as the VP of Special Projects, Desktop Metal, a company involved in 3D printing. He is a fellow of ASM International and APMI International. He was the Divisional Editor for the section on Metal Injection Molding for ASM Handbook, Volume 7 (Powder Metallurgy), 2015. He has served as the co-chair for the MPIF MIM Conference, Powdermet, and is the founding co-organizer of Tungsten, Refractory, and Hardmaterials Conference Series. He is the Tech Board representative for the Association of Metal Additive Manufacturing (AMAM) and is the Chair for the AMAM Standards Committee. He will be serving as the Co-chair for the AMPM2022 at Portland, OR.
Pre-Sinter Rework of Green Parts to Eliminate Molding Defects of MIM Parts
Caleb Spencer, ARC Group Worldwide
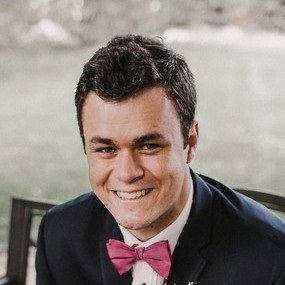
Caleb Spencer has been involved in both the plastics and metal injection molding industry during his 5 year career. Caleb serves as a project engineer at ARC Colorado and primarily works with the firearms industry. Before joining ARC Colorado, Caleb worked as a New Product Development Engineer for Nordson Medical. He received a Bachelor of Science in Mechanical Engineering with a Minor in Mathematics from LeTourneau University.
Extrusion-Based Additive Manufacturing (EAM) of Nickel-Titanium Shape Memory Alloy via Bio-Based Polymer
Hong Wang, Université de Franche-Comté, FEMTO-ST institute
Hong WANG received the B.S. degree in Process Equipment and Control Engineering from Xi’an Jiaotong University, Xi’an, China, in 2016 and the Engineer diploma and M.S. degree in Mechanical Engineering from University of Technology of Troyes (UTT), Troyes, France, in 2019. He is currently working toward the Ph.D. degree in manufacture of porous NiTi alloy structure via material extrusion additive manufacturing with UTT & Department of Applied Mechanics of Institute FEMTO-ST (Besancon, France).
The Relationship between Molding Variables, Green Part Quality Indicators, and Final Sintered Shrinkage Part Quality
Gustavo Mosquera, SIGMA Plastic Services, Inc
Lithography-Based Metal Manufacturing (LMM)
György Attila Harakaly, Incus GmbH
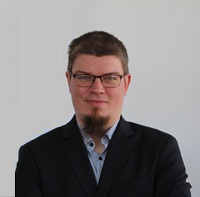
Dr. György Harakály is the Head of R&D Materials at Incus GmbH, an Austrian system provider for an innovative lithography-based Metal Manufacturing (LMM). He obtained his B.S and M.S. degrees in the Budapest University of Technology and Economics in the fields of chemical engineering and pharmaceutical engineering. Afterwards, he received his Ph.D degree from Technische Universität Wien, Austria, where his research was focused on the development of photopolymerizable resins for the AM of dental applications. Since 2021 he is responsible for the research and development at Incus, bringing his expertise in polymer chemistry, material science and additive manufacturing.
Simulating Sintering Shrinkage and Distortion for Production Success
Andrew Roberts, Desktop Metal
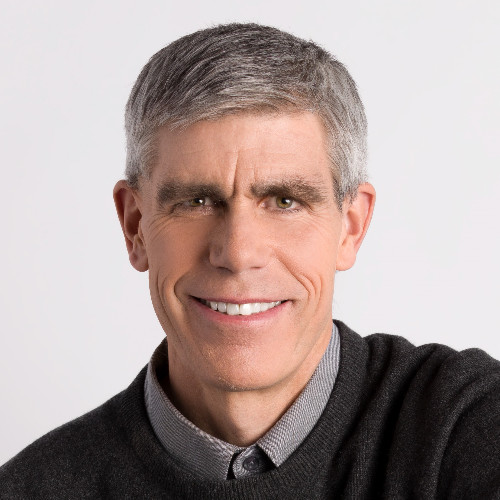
Andy Roberts is the inventor of two products at Desktop Metal in the generative design and simulation space. The first, Live Parts™, is a generative design tool that uses morphogenetic principles to enable engineers and designers to quickly realize the benefits of additive manufacturing. The second product, Live Sinter™, simulates sintering of powder metal parts, and transforms geometry to counteract the effects of distortion. A graduate of Harvard University and Massachusetts Institute of Technology with extensive experience at leading technology innovators such as Parametric Technology Corp., Ab Initio, and IBM, Andy has a proven track record of bringing to market successful products for engineers and developers.
Review of the MIM Industry in Europe
Paul A Davies, Sandvik Additive Manufacturing
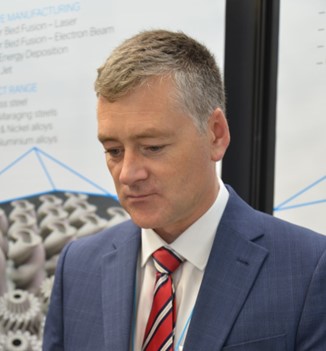
Studied physics in Swansea University , in Wales, U.K. and completed a PHD in the field of Material Science. Five years’ experience in steel industry working in the automotive and defence sectors and has worked for Sandvik Additive Manufacturing for more than 15 years in a technical sales capacity, specialising in powder metallurgy with a particular focus on Metal Injection Moulding and Additive Manufacturing.
Influence on MIM Properties of Different Particle Size Distribution of Special Water Atomized Fine Powder
David Shore, Höganäs AB
Impact of Gas Guiding and Advanced User-Friendly Binder Handling Solutions for MIM and AM Furnace Product Line: CFD Simulation, Customer Feedback and Binder Handling Solutions
Maximilian Mungenast, Carbolite Gero GmbH & Co. KG
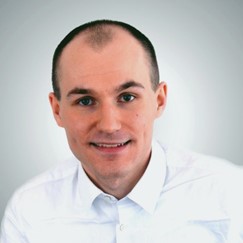
Max received BS in Mechanical Engineering / Product Development at the University of Pforzheim. Upon completion of his studies, Max continued as an academic employee at Pforzheim University’s Institute for Precious and Technology Metals,. His work expereinces and activities include materials science, magnetic recycling, co-development of a metal 3D printing process. In 2022, Max joined Carbolite Gero GmbH & Co. KG and is currently workign in an international sales and product developmentsales role as the export area sales manager.
CASE STUDY: Utilizing Metal Injection Molding and AM Binder Jetting in the Production of a 316L Industrial Part
Gaetano Mariella, Polymer Technologies Inc.
Gaetano (Guy) Mariella is a veteran of material science and metallurgy with over three decades of engineering experience designing solutions for the military, aerospace, medical, and electronics industries.
Currently the Chief Technology Officer and Director of Engineering at PTI in Clifton, New Jersey, which offers precision integrated injection molding services, Guy leads the engineering team in developing and delivering best-in-class products that leverage the advantages of combining both engineering polymers and metals.
His innovative thinking and development of refractory powder metal techniques and parts have helped hundreds of clients—from Boeing, to the US Military, to major healthcare providers—solve complex problems and have led to the creation of groundbreaking medical devices and mission-critical military hardware.
Prior to PTI, Guy’s work in powdered metals engineering includes over 20 years of experience at Bayer Material Science and HC Starck Inc. (formerly Kulite Tungsten Corporation) where he served as Director of Process Control and Development. In this role, he was responsible for production and process control, new process creation, and research and development. He spent another 10 years at Kulite Semiconductor Products Inc. where he served in multiple roles including Director Supply Chain, Senior Manufacturing engineer and Program Manager.
A leader in the field, he has presented several papers at major conferences and holds multiple patents He estimates that throughout his career he has sintered over 30 million lbs. of powder metal products.
He received his degree in Metallurgy and Material Science from NYU Tandon / Brooklyn Polytechnic.
Effect of Feedstock, Filament, and Green Part Characteristics on Sintered Properties of Material Extrusion (MEX) 3D Printed Copper
Kameswara Pavan Kumar Ajjarapu, Ph.D. Candidate, University of Louisville
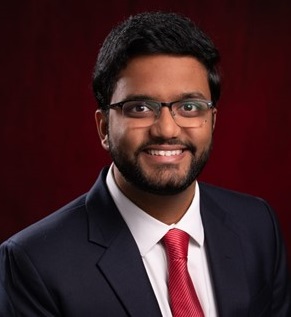
Pavan is a Ph.D. candidate in Mechanical Engineering at the University of Louisville. His research focusses on processing and fabricating non-ferrous metal alloys using powder fused filament fabrication 3D printing. He leverages his materials science background to apply the structure-property-processing correlationship to 3D printing.
Additionally, he works with Minority Business Development Agency (MBDA) as a part of an initiative by the Department of Commerce, towards uplifting minority-owned business enterprises through the Advance Manufacturing Center in Kentucky.
Binder System for Powder Injection Molding of NdFeB Permanent Magnets
Vahid Momeni, Institute of Polymer Processing of the Montanuniversitaet Leoben
Vahid Momeni works as a researcher and PhD student at Montanuniversitaet Leoben in Austria. He has been involved in different projects at the additive manufacturing group, institute of polymer processing. Currently, he is developing feedstocks for injection and 3d-printing of sensitive alloys such as aluminium and permanent magnets. He has published 2 books and several articles in the MIM and additive manufacturing fields.
Performance of Highly Uniform High Density Multimodal Stainless Steel Powders in Metal Injection Molding
Joseph Schramm, Uniformity Labs
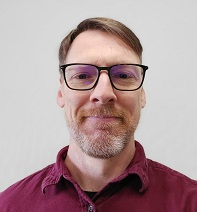
Joseph Schramm is the Director of Materials Development at Uniformity Labs.
His PhD is from California Institute of Technology, and his MS, and BS from Iowa State University. He has worked for more than a decade leveraging and engineering the emergent properties of random systems to develop technologies that push the limits on the capabilities manufacturing processes.
Tungsten Carbide PM Products in High Precision and High-performance Engineered Tooling and Wear Solutions
Jeffrey Taylor, Crafts Technology, A Hyperion Materials & Technology Company
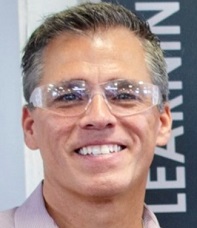
Jeffrey Taylor is the President of Crafts Technology, which is part of the Precision Solutions group of the Hyperion Materials & Technology (HMT) company. While HMT is a leader in advanced materials with decades of experience developing and manufacturing tungsten carbide powder, cemented carbide, industrial diamond, and cubic boron nitride, Crafts Technology and the Precision Solutions group specializes in the conversion of the powdered metallurgy products into finished high precision and high-performance engineered tooling and wear solutions.
Jeff’s 36-year professional career includes having worked in a variety of roles, including toolmaker and then manufacturing manager at New England Carbide, sales and sales management at A.W. Chesterton, and then ultimately as President of Crafts Technology, one of the world’s oldest continuously operated companies of its’ kind in the world. Each of these respective companies all specialize in the design and production of engineered wear solutions, cutting tools, and/or fluid handling & control products where powdered metallurgy, in the form of tungsten carbide, advanced ceramics or diamond matrices, is a core competency.
Jeffrey’s education includes an AS in Manufacturing Engineering Technology as well as a Bachelor of Manufacturing Management obtained from the University of Minnesota.
Some additional accomplishments:
1. Previously presented at The American Pulp & Paper Association (TAPPI), Water Environment Federation (WEF), Marcus Evans Hydropower Maintenance & Reliability Conference….and many other venues.
2. Past “Chairman of Certification”: Society of Manufacturing Engineers (SME NS Chapter) and Advisory Council Member for National Institute of Metalworking Skills (NIMS)
3. Three patent pending innovations including a brazed carbide tip Automated Fiber Placement [AFP] cutter/blade, a CraftAlloy™ diamond nozzle for fluid dispensing and a CraftAlloy™ diamond capillary.
Outside of work, Jeffrey is the father of two daughters, 16 and 21 years old. The oldest of which is enrolled in an Advanced Manufacturing Degree/Apprenticeship program at Harper College. His hobbies include traveling, skiing, rollerblading, mountain biking, running and he is a PADI certified Rescue Diver.
Development of Flexible Magnetic Micropillar Actuator via Powder Injection Molding
Jin Wook Park, Korea Institute of Materials Science
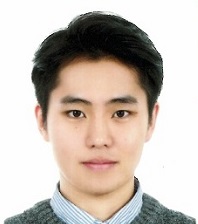
Jin Wook Park is a graduate student with Ph.D. Da Seul Shin's research group at KIMS, and Prof. Sang Min Park’s research group at Pusan national university. His research fields are concentrating on the fabrication of magnetic soft composites using injection molding technology. As evolving the industrial applications, he aims to develop a manufacturing process for the mass production of soft composites which was responsive to the magnetic field. In addition, he is interested in fundamental modeling, numerical simulation, and artificial intelligence for a broad area of powder metallurgy such as conventional powder metallurgy, powder injection molding, and additive manufacturing. He submitted a paper on magnetic soft micropillar arrays. He is also an active participant in domestic and international conferences such as Korea Powder Metallurgy Institute, ISNNM, and MIM.
Beyond Binder Jetting – Alternate Sinter Based AM Technologies
Benjamin Arnold, Tritone Technologies

Ben Arnold is Tritone Technology’s VP of Business Development for North America. Ben has worked in the Additive Manufacturing industry since 2006 and with Metal Additive since 2016. He has helped several major OEMs bring new technology platforms to market across polymer, metals, and composite materials. In his current role, Ben is introducing Tritone’s proprietary Moldjet technology to North American Market. Moldjet is a paste format sinter based additive technology that is applicable to both metals and ceramics. Ben holds Bachelor of Science degree in Mechanical Engineering from WPI and MBA from Northeastern University. He was recognized recently for his work in the Additive Manufacturing industry with a DINO award from the AM User Group.
Printable Filament Design of 316L Stainless Steel Master Alloys
Marina ValeroRodrigo, University of Castilla La Mancha
The Missing Link of MIM
Lucas Logan, ARC Group Worldwide
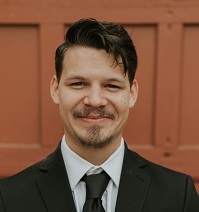
Lucas Logan has been involved in several areas of the manufacturing industry during his five-year career. Lucas serves as Quality Engineer at ARC group worldwide. Prior to joining ARC group, Lucas worked in production management at a plastics injection molding firm and as a process designer at a precision grinding company. He received a Bachelor of Applied Mathematics with a concentration in Computer Science from the University of Northern Colorado.
How Ti BJP Compliments Ti MIM
Victor Villarini, TriTech Titanium Parts
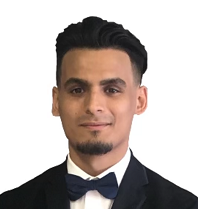
Victor Villarini is Engineering Manager at TriTech Titanium Parts LLC.
He is a Mechanical Engineer from Wayne State University in Detroit, Michigan. His work includes engineering solutions for three net shape production processes: Investment casting, 3D binderjet printing, and metal injection molding. All for titanium. He has been an integral part of the startup of TriTech’s operations, as well as the process improvements required to make high quality titanium parts. Most recent accomplishments include overseeing the start-up and development of the first Grade 5 Titanium binder jet printing process. He has been a leader with his work at TriTech and has made significant advances with this new technology.
Additive Manufacturing of Aluminum Alloy by Metal Fused Filament Fabrication (MF3)
Sihan Zhang, Univeristy of Louisville
Sihan Zhang is a PhD candidate at University of Louisville in Dr. Atre’s Materials Innovation Guild. He received his MS degree from Arizona State University and BEng degree from Zhejiang University. He is currently working on developing Metal Fused Filament Fabrication (MF3) technology. His current research focuses on applying Al alloy in MF3 process for metal additive manufacturing. He plans to work in additive manufacturing industry to develop materials and processing after graduation.
Metal Additive Manufacturing by Continuous De-Bind and Sintering of Binder Jetted Products
Stephen L. Feldbauer, Dir. Research and Development, Abbott Furnace Co.
Dr. Feldbauer received his Ph.D. in 1995 from Carnegie Mellon University in Materials Science and Engineering. He joined Abbott Furnace Co in 2002 where he is currently the Director of Research and Development. Dr. Feldbauer is also a Senior Adjunct Faculty member in Engineering at the Pennsylvania State University. He is the author of numerous articles, publications, and has been awarded eight patents. He is an active member of the MPIF, American Welding Society’s C3 Committee, and Automotive Industry Action Group on Brazing.
Additively Manufactured Metal Heat Exchangers for Energy Applications
Julio Izquierdo, University of Louisville
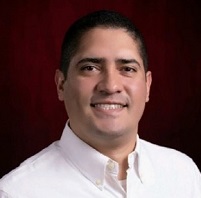
Julio Jair Izquierdo PhD candidate, University of Louisville.
MS from the University of Louisville
BS from the university of Louisville
He is currently a PhD candidate in mechanical engineering and is a member of the Pyro-Electric Research Lab (PERL). His research focuses on the modeling and testing a variety of 3D printed geometries for the improvement of high temperature heat exchangers with its main focus on solar power plants. As a graduate student, he was selected by the committee of mechanical engineering professors as the first awardee of the Ed Toutant fellowship in 2022. He currently works as a manufacturing engineer for an aerospace company where he fabricates carbon-nan-tube-based sensors for the US air force. In his free time, he enjoys SCUBA diving and photography.